Properties and Uses of Carbon Steel
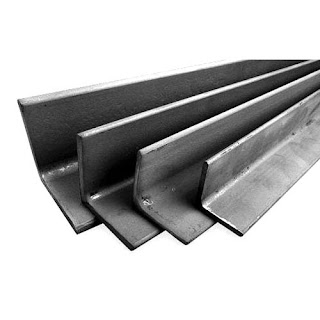
Properties and Uses of Carbon Steels: Mild Steel 1. Mild Steel: Carbon content between 0,1% and 0,3%. Properties: Less ductile but harder and tougher than iron, grey colour, corrodes easily. Uses: Girders or beams, screws, nut and bolts, nails, scaffolding, car bodies, storage units, oil drums. Medium Carbon Steel 2. Medium Carbon Steel: Contains between 0,3% and 0,7% carbon. Properties: Harder and fewer ductile than low-carbon steel , tough and have a high lastingness . Use: It's used for the manufacture of products which have to be tough and hard wearing like gears, tools, keys, etc. High Carbon Steel 3. High Carbon Steel: Contains between 0,7% and 1,3% carbon. Properties: Very hard and brittle material. Uses: It's used for cutting tools and products which have to withstand wear such as guillotine, springs, etc. Stainless Steel 4. Stainless steel: are iron and ch